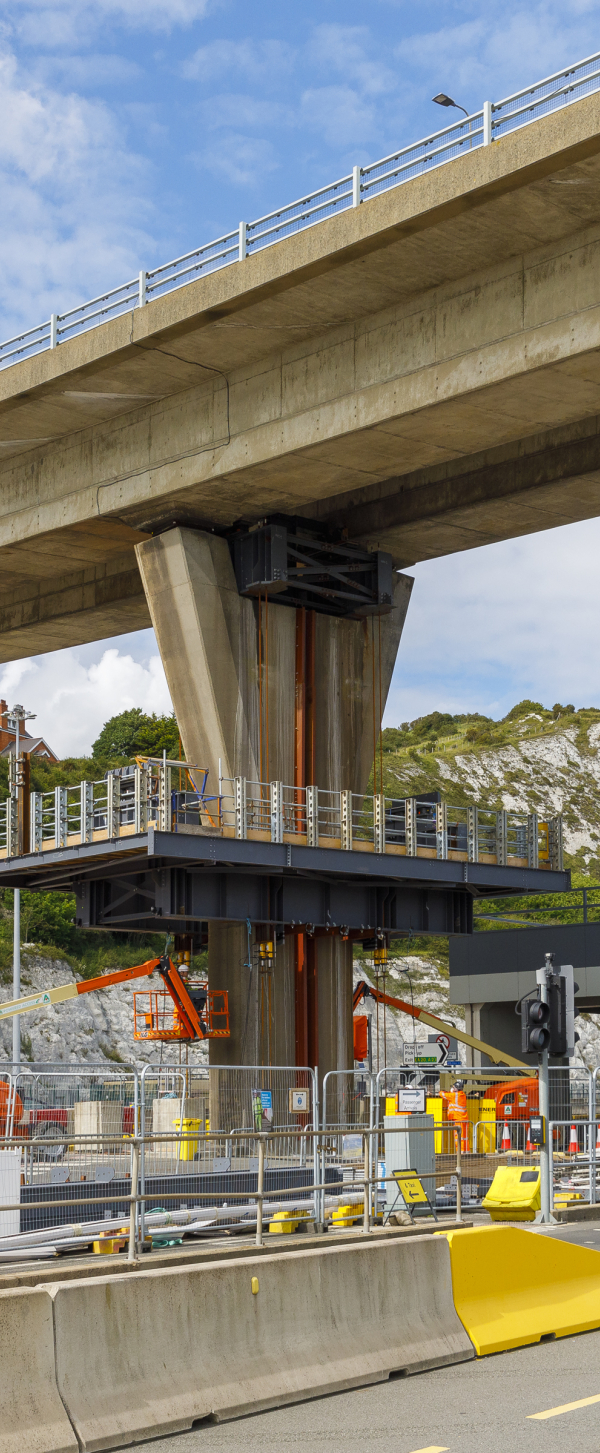
East Cliff Viaduct
VolkerLaser was contracted to undertake bearing replacement and associated works, including jacking and temporary works, on the East Cliff Viaduct in Dover.
What we did
The East Cliff Viaduct is a seven span, 348m long viaduct connecting the A20 at promenade level to the A2 on the cliffs. It carries a 3-lane carriageway (of varying width) and 2m wide footways on each side. In plan the structures comprise a 1015m radius circular curve which carries a three lane, 10m carriageway over the first three spans, widening along a transition curve on Span 4, to a three lane, 12m wide carriageway along a 117.5m radius circular curve over Spans 5 to 7.
The structure was originally constructed in 1976, but due in part to age and the costal conditions, the bearings were identified as requiring replacement. The bearings across all piers were showing significant deterioration, primarily through corrosion.
Building upon our existing relationship with the Port of Dover, our specialist team initially undertook 8 months of ECI work including structural monitoring, temporary works design including the development and fabrication of the temporary works solution and the designing of a jacking system to deal with the unequal loading of the structure during jacking, along with ongoing monitoring of the bridge.
All six piers on the viaduct required bespoke temporary works systems to facilitate the replacement of the existing non-functioning bearings. As well as the bearings replacement, the scope of works included the reconstruction of the bearing plinths and localised concrete repairs to the top of the piers. Deck drainage was also to be reinstated where disturbed by the other works.
At the lower piers, a trestle system has been designed to bear directly onto the pile cap. At the taller piers, a high-level solution was required to minimise disruption to the port. As a result, a hanger frame solution was developed. The 50-tonne hanging frame was constructed at ground level on four concrete plinths, and the hanger beams, which connect the frame to the structure, were pre-installed onto the pier support 13m above the hanging frame.
The hanger beams and hanging frame were connected using eight Dywidag bars, with each bar having a 60-tonne hydraulic jacking assembly. All eight jacks were energised simultaneously and raised the hanging frame to the underside of the hanger beam in 250mmm increments. The frame needed to be lifted within a tolerance of +/=1mm, which was achieved by controlling each jack using a synchronised lifting system. The full operation took two days to complete the lift, with a further day to connect the hanging frame to the hanger beams.
The project encountered complex and unexpected engineering issues throughout, and at all times our specialist team generated innovative and advanced engineering solutions and processes. Despite this, there was a significant extension to the original programme, but this was effectively and efficiently managed with our operational and commercial teams.
Constant communication and collaboration with the wider VolkerLaser team, as well as National Highways and Costain was key to ensuring the project was delivered successfully.
"This project and the team has had to contend with an assortment of unexpected challenges and constraints be it existing conditions being widely different than expected, water cascading over the piers, and hidden asbestos, to name a few. Not only were these resolved in a very agile manner by the collaborative team including, the Port of Dover, designers, National Highways, VolkerLaser and others but they learned from these quickly, mitigating those risks for the remainder of the works completing three months ahead of the extended schedule and under budget."
Marcus Hollan Senior project manager, Costain