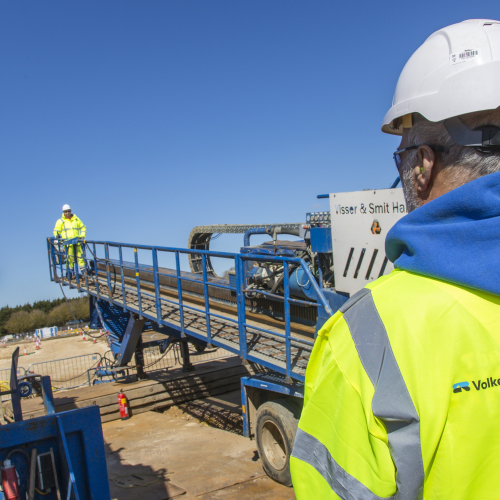
VolkerTrenchless Solutions wins UKSTT Award for Innovation
VolkerTrenchless Solutions (Visser & Smit Hanab) has won the 2018 UKSTT (United Kingdom Society for no dig Trenchless Technology) Awardfor Innovation for its Mongstad horizontal directional drilling (HDD) landfall project.
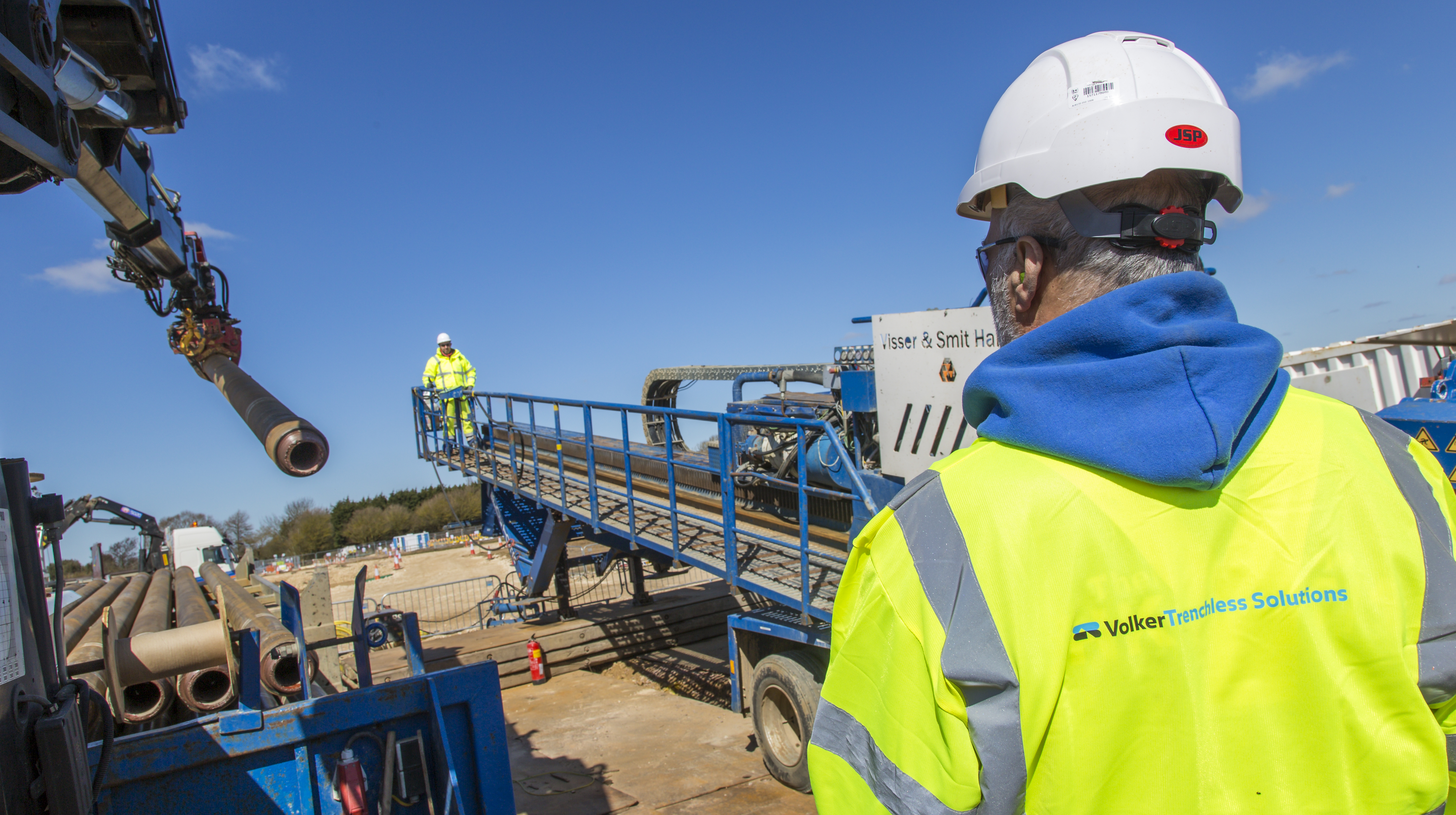
The Awards recognise industry best practice and cover a range of excellence, including innovation, renovation, environmental performance and application of digital technology.
The project, executed for the Norwegian company Statoil (now Equinor), is a crucial part of the pipeline route where the crude oil pipeline comes ashore into the Mondstad oil refinery from a newly discovered oil field in the North Sea.
The team was tasked with drilling an 800-metre-long, 1.2 metre diameter borehole, in hard rock formation.
Producing 12 million barrels per year into the Mongstad oil refinery, the sub-sea pipeline had to be installed through the rock formation, exiting at 300 metres below sea level.
Using a HDD rig on a project of this scale had never before been attempted. As a result, this was the most complex and innovative project undertaken by VolkerTrenchless Solutions, or any other trenchless drilling organisation to date.
Innovation
- Traditional HDD methods of installation would not be possible for this project, given the makeup of the hard rock layers of the shoreline’s rock face
- With the foreshore only 100 metres away, and with an exit point 300 metres below sea level, the team had to use adjusted HDD technology to allow the 915mm pipeline to be installed along the HDD route
- Combined with the steep entry angle of 24.5 degrees, and the exit point at a depth of approx. 315 metres below the sea level, the challenge was more difficult. VolkerTrenchless Solutions engineered a solution where the drilling rig could be mounted onto a steel frame construction, to enable the entry angle to be achieved
- The team had to use specially manufactured hole openers, to expand the diameter of the initial pilot bore up to 1.2 metres in diameter from the entry side. This was to ensure the drill pipe could withstand the forces exerted, as it was rotated through the rock hundreds of metres below the ground
- Due to the depth and size of the bore, forward reaming was the only viable option, with the team having to calculate fatigue factors on the drill pipe used for the forward reaming operation
Despite several challenges, the project was completed on time and to budget.